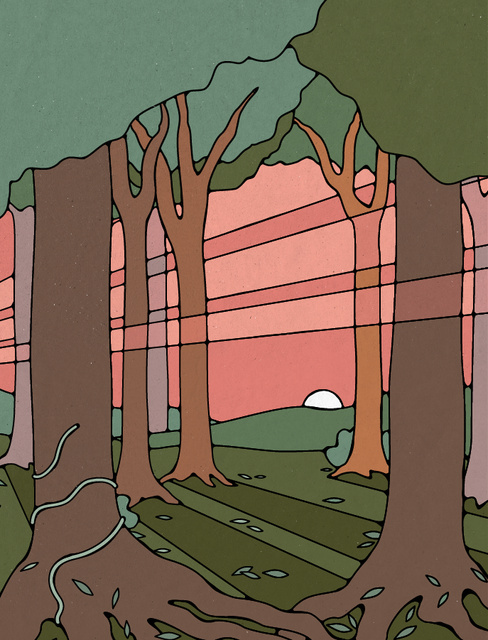
Sourcing Our Foam: The Story of Sri Lanka
We went straight to the source and partnered with local experts to build our own fair trade network and foam rubber factory.
Natural foam rubber is pretty amazing, really. Take milky sap from a rubber tree, spin it really fast to get the water out, mix it with small amounts of compounds to help the molecules bind together, pour it into a mold, bake it at 212 degrees for an hour, and ta-da: you have a squishy white square you can sleep on.
When we first got into bedding, we traced the highest-quality natural rubber in the world to its source: Sri Lanka. We partnered with a local rubber supplier and specialist, Januka Karunasena, and cut out the middlemen to source our foam from him directly.
But that wasn’t enough. The more we learned about the rubber industry, and the more people we met in Sri Lanka, the more room for improvement we found. To make the mattresses of our dreams, we needed to control every part of the supply chain, from the rubber tree to the factory, so we could ensure quality control and fair treatment of workers every step of the way.
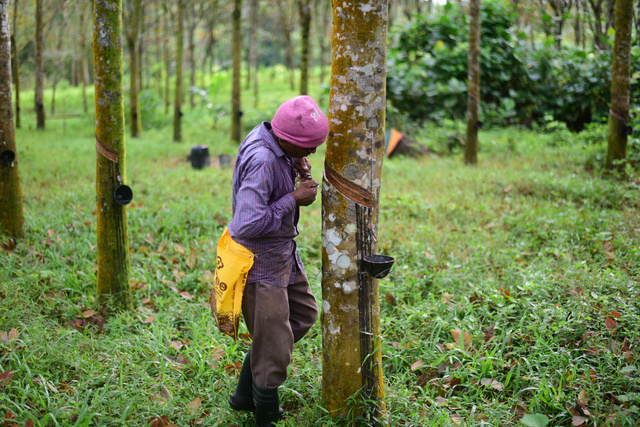
Our Fair Trade Network
Rubber tree forests are beautiful and highly sustainable. One tree can supply sap (liquid latex) for over 20 years and rubber trees have one of the highest carbon dioxide absorption rates. When we first started sourcing it, the rubber industry in Sri Lanka was dying. It was hard for farmers to compete with cheaper crops, even if they weren’t good for the land or the local economy.
With Januka spearheading the project, we built a Fair For Life certified fair trade network of 323 small organic rubber farmers. It’s the largest in Sri Lanka, employing more than 1,700 workers. And we’ve been able to ensure fair wages and working conditions for all of them.
Our farms are also certified organic, which reduces water and energy use and boosts the biodiversity of the forests. Other brands pay a surcharge on organic that often only goes to the processing facilities. We are the processing facility, so our premiums benefit the tappers and farmers directly.
I led a team to turn a declining natural foam rubber business into one that is sustainable and grows.
- Januka Karunasena, CEO
The Earthfoam Factory
After we collect rubber tree sap from our fair trade network of farmers, it’s processed at our shiny new factory in Colombo, Sri Lanka. It’s the only place in the world that makes Earthfoam.
Before we opened our own factory, we sent the sap to be processed in Malaysia. Making foam rubber in the same place it’s harvested has reduced energy and transportation costs and allowed us to have a greater impact on our workers.
We have 200 people working at our factory, ranging from highly experienced foam rubber experts to construction workers who helped build the factory and wanted to stick around and learn how to make mattresses instead.
We’re also able to attend meetings with our tappers, we hear directly from our farmers, and we’re part of the local community and economy.
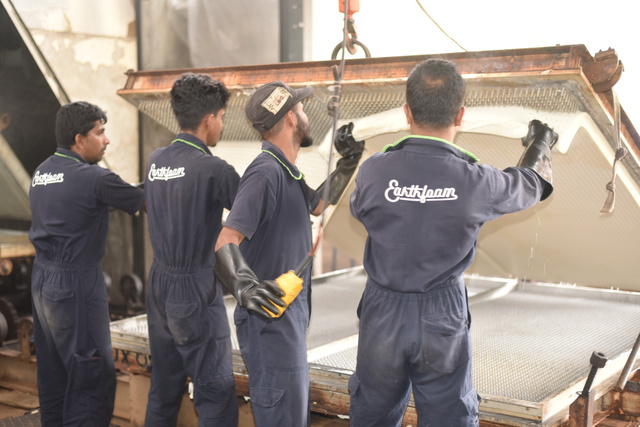
I am very happy to be a part of this factory. We make a good product not only for us but for the rest of the world. And we’re in beautiful surroundings.
Manjula Kumara, Executive: Foam Production
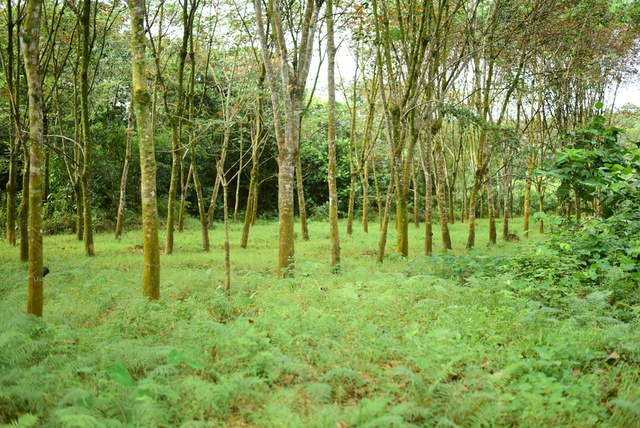
Putting it All to Bed
Because rubber is a natural material, it has natural variance. Where factories making synthetic foam can use the exact same formula and process with every batch, there’s a lot of nuance and chemistry that goes into processing our foam. We use our own recipe - one that was created specifically based on our high quality standards and the knowledge of Januka and his team.
First, the centrifuge machine operators separate non-rubber content from the sap and monitor the rubber as it matures. Compounding specialists add binding ingredients, and the foam is aerated to create a unique bubble structure. Then the rubber is vulcanized, changing from a frothy liquid into a bouncy block of foam. The steam used to vulcanize our rubber is maintained by a boiler fed with rubber tree wood. This wood is harvested as part of routine uprooting during the re-plantation process.
The last step before our foam is shipped to our Chicago factory is quality control. Every slab is tested for firmness, durability, and any defects. (People like this job because our foam feels so nice.)
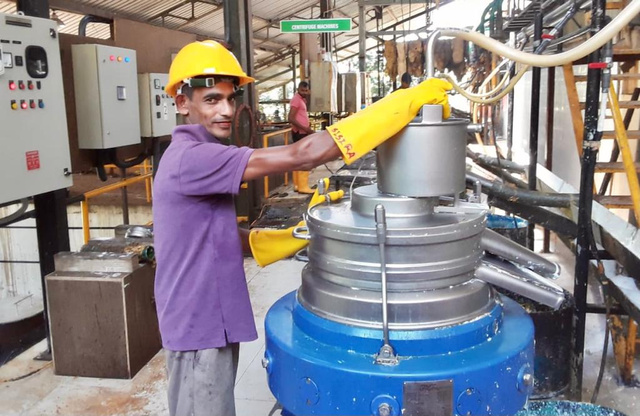
Earthfoam isn’t just any natural foam rubber. We think it’s the best in the world. It’s a material that is ethically sourced and thoughtfully made with the wellbeing of all of our workers and our world in mind.